Os discos de desbaste desempenham um papel fundamental em diversos setores, facilitando a modelagem e o acabamento de materiais. No entanto, como qualquer outra ferramenta, eles não estão imunes a problemas que podem prejudicar sua eficiência e desempenho. Neste artigo, abordaremos os problemas comuns com discos de desbaste, exploraremos suas causas e forneceremos soluções eficazes para um fluxo de trabalho perfeito.
Introdução
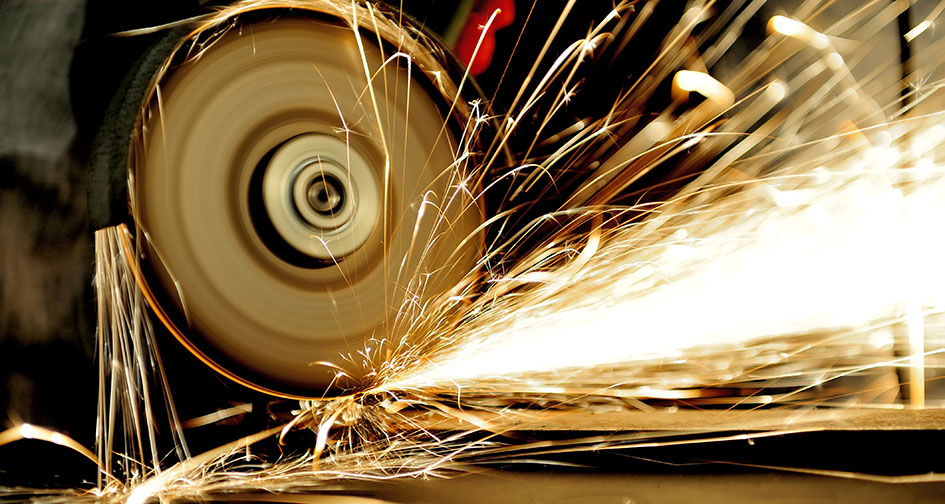
Os discos de desbaste desempenham um papel fundamental em diversos setores, servindo como ferramentas essenciais para processos de remoção de material, modelagem e acabamento. Entender sua definição, importância em diferentes setores e os problemas comuns enfrentados é crucial para otimizar seu uso e garantir operações eficientes.
A. Definição de Discos de Moagem
Discos abrasivos são ferramentas abrasivas utilizadas em processos de usinagem para cortar, retificar ou polir superfícies de materiais. Esses discos normalmente consistem em partículas abrasivas unidas a um material de suporte, criando uma ferramenta rotativa que pode remover o excesso de material, alisar superfícies ou afiar arestas. Eles estão disponíveis em diversos formatos e tamanhos, cada um projetado para aplicações específicas.
B. Importância em vários setores
Indústria metalúrgica:
Na fabricação e manufatura de metais, os discos de desbaste são essenciais para moldar, rebarbar e dar acabamento a superfícies metálicas. Eles são comumente usados com esmerilhadeiras angulares para obter dimensões precisas e qualidade de superfície.
Indústria da Construção:
Profissionais da construção contam com discos de desbaste para tarefas como preparação de superfícies de concreto, alisamento de bordas ásperas e remoção de imperfeições em materiais como pedra e concreto.
Indústria automotiva:
Discos abrasivos são essenciais no setor automotivo para tarefas que vão desde afiar ferramentas até moldar e dar acabamento a componentes metálicos. Eles contribuem para a precisão e a qualidade das peças automotivas.
Indústria da Madeira:
Marceneiros utilizam discos de desbaste para moldar e alisar superfícies de madeira. Esses discos são eficazes na remoção de excesso de material, no refinamento de formas e na preparação da madeira para acabamento posterior.
Fabricação Geral:
Os discos de desbaste encontram aplicações em vários processos de fabricação onde é necessária a remoção precisa de material, contribuindo para a produção de componentes de alta qualidade.
C. Problemas comuns enfrentados
Desgaste e abrasão do disco:
O uso contínuo pode causar desgaste e abrasão do disco de desbaste, afetando seu desempenho. Inspeções e substituições regulares são necessárias para manter a eficiência.
Superaquecimento:
O atrito excessivo durante o uso prolongado pode levar ao superaquecimento, afetando a durabilidade do disco e a qualidade da superfície acabada. Medidas adequadas de resfriamento e pausas periódicas são essenciais.
Entupimento:
Os discos de desbaste podem acumular resíduos de material, reduzindo sua eficácia. A limpeza regular ou a escolha de discos com recursos antientupimento ajudam a prevenir esse problema.
Vibração e oscilação:
Desbalanceamentos ou desgaste irregular podem resultar em vibração ou oscilação, afetando tanto a qualidade do acabamento quanto a segurança da operação. Instalação e balanceamento adequados são essenciais.
Seleção de disco incorreta:
Escolher o tipo errado de disco de desbaste para um material ou aplicação específica pode levar à ineficiência e a possíveis danos. A seleção adequada com base na compatibilidade do material é essencial.
Compreender a definição, a importância e os potenciais desafios associados aos discos de desbaste é essencial para as indústrias que dependem dessas ferramentas. Ao abordar problemas comuns e garantir o uso adequado, as indústrias podem maximizar a eficácia dos discos de desbaste em suas respectivas aplicações.
Desgaste em discos de moagem
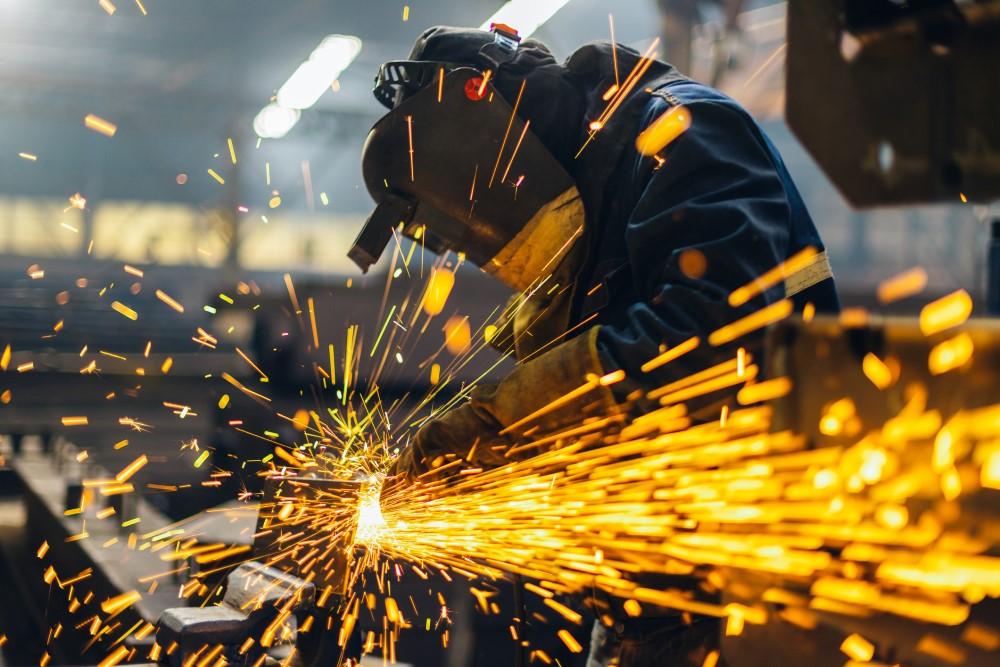
Discos de desbaste são ferramentas essenciais em diversos setores, proporcionando a abrasão necessária para tarefas que vão da fabricação de metais ao polimento de concreto. Compreender os fatores que contribuem para o desgaste dos discos de desbaste é crucial para otimizar seu desempenho e garantir a segurança.
Dureza e composição do material:
Variação de dureza:Os discos abrasivos encontram materiais com diferentes níveis de dureza. Materiais abrasivos como metal e concreto podem variar significativamente em dureza. O esmerilhamento contínuo em materiais duros acelera o desgaste.
Composição do material:A presença de elementos abrasivos no material a ser retificado pode impactar o desgaste do disco de retificação. Partículas abrasivas podem acelerar o desgaste do disco.
Pressão e força de moagem:
Pressão excessiva:Aplicar pressão excessiva no disco de desbaste pode levar a um desgaste mais rápido. É essencial usar a pressão recomendada para a aplicação específica para evitar tensão desnecessária no disco.
Força inadequada: Por outro lado, força insuficiente pode resultar em desgaste prolongado, gerando atrito e calor adicionais, contribuindo para o desgaste.
Qualidade e composição do disco:
Qualidade do material abrasivo:A qualidade do material abrasivo utilizado no disco de desbaste influencia significativamente sua vida útil. Materiais abrasivos de alta qualidade tendem a resistir ao desgaste e a manter o fio afiado por mais tempo.
Agente de ligação:O agente de ligação que mantém as partículas abrasivas unidas desempenha um papel crucial. Um agente de ligação bem projetado aumenta a durabilidade do disco.
Condições do ambiente de trabalho:
Temperatura:As temperaturas elevadas geradas durante o desbaste podem afetar a composição do disco. O calor excessivo enfraquece o agente de ligação e acelera o desgaste.
Umidade e contaminantes:A exposição à umidade ou contaminantes no ambiente de trabalho pode afetar a integridade do disco de moagem, causando desgaste mais rápido.
Técnica do Operador:
Técnica adequada:A habilidade e a técnica do operador são vitais. O uso inadequado, como esmerilhamento em ângulos incorretos ou uso de força excessiva, pode contribuir para o desgaste irregular e reduzir a longevidade do disco.
Inspeções regulares:Os operadores devem inspecionar regularmente o disco de desbaste em busca de sinais de danos ou desgaste. Discos que apresentem desgaste além de um certo ponto devem ser substituídos imediatamente.
Compatibilidade de tamanho de disco e RPM:
Tamanho correto:Usar o tamanho correto de disco para o moedor é crucial. Discos de tamanho incorreto podem apresentar desgaste irregular ou representar riscos à segurança.
Compatibilidade RPM:A observância das rotações por minuto (RPM) recomendadas para o disco de moagem garante um desempenho ideal e evita o desgaste prematuro.
Manutenção regular, cumprimento das condições operacionais recomendadas e seleção do disco de desbaste adequado para cada tarefa são práticas essenciais para minimizar o desgaste. Ao compreender os fatores que influenciam o desgaste, os operadores podem aumentar a longevidade e a eficiência dos discos de desbaste, contribuindo para operações de desbaste mais seguras e produtivas.
Moagem irregular
Desbaste irregular refere-se à situação em que a superfície a ser desbastada não obtém um acabamento consistente e liso. Esse problema pode surgir por diversos motivos e afetar a qualidade da peça. Aqui estão os fatores comuns que contribuem para o desbaste irregular e possíveis soluções:
Seleção incorreta de rebolo:
Solução:Certifique-se de que o rebolo seja adequado ao material a ser lixado. Diferentes materiais exigem propriedades abrasivas específicas. Escolha o tipo de rebolo, o tamanho do grão e a liga adequados para a aplicação.
Polimento inadequado das rodas:
Causa:Uma roda de desbaste que não esteja adequadamente lixada pode causar desgaste irregular e corte ineficaz.
Solução:Lixe regularmente o rebolo para manter sua forma e remover qualquer resíduo acumulado. A lixagem adequada garante uma superfície de corte consistente.
Fluido de moagem ou refrigerante inadequado:
Causa:O uso insuficiente ou impróprio de fluido de moagem pode resultar em aumento de atrito e calor, levando a uma moagem irregular.
Solução:Utilize um fluido de retificação ou refrigerante adequado para dissipar o calor e reduzir o atrito. O resfriamento adequado é essencial para obter resultados uniformes.
Parâmetros de moagem incorretos:
Causa:O uso de parâmetros de retificação incorretos, como velocidade excessiva, taxa de avanço ou profundidade de corte, pode levar a uma retificação irregular.
Solução:Ajuste os parâmetros de moagem de acordo com os requisitos do material e da aplicação. Consulte as recomendações do fabricante para obter as configurações ideais.
Roda de desbaste gasta:
Causa:Uma roda de desbaste desgastada pode não proporcionar uma superfície de corte consistente, resultando em desbaste irregular.
Solução:Substitua o rebolo quando ele atingir o fim de sua vida útil. Inspecione-o regularmente em busca de sinais de desgaste.
Pressão ou taxa de alimentação irregulares:
Causa:Pressão irregular ou taxas de avanço inconsistentes durante a moagem podem levar à remoção irregular do material.
Solução:Aplique pressão uniforme e mantenha uma taxa de avanço consistente em toda a peça. A habilidade do operador e a atenção aos detalhes são essenciais.
Problemas com a máquina:
Causa:Problemas mecânicos com a retificadora, como desalinhamento ou problemas com o eixo, podem resultar em retificação irregular.
Solução:Realize verificações de manutenção regulares na retificadora. Resolva quaisquer problemas mecânicos imediatamente para garantir o funcionamento adequado.
Fixação da peça de trabalho:
Causa:Peças de trabalho mal fixadas ou desalinhadas podem causar um desbaste irregular.
Solução:Garanta a fixação e o alinhamento adequados da peça de trabalho. Fixe-a firmemente para evitar movimentos durante o processo de retificação.
Para lidar com a retificação irregular, é necessária uma combinação de configuração adequada do equipamento, parâmetros operacionais corretos e práticas regulares de manutenção. Os operadores devem ser treinados para identificar e corrigir problemas prontamente, a fim de obter resultados consistentes e de alta qualidade em aplicações de retificação. Inspeções regulares e a adesão às melhores práticas contribuem para uma remoção eficiente e uniforme do material durante o processo de retificação.
Problemas de superaquecimento
O superaquecimento durante o desbaste é um problema comum que pode afetar o desempenho tanto do rebolo quanto da peça de trabalho. O calor excessivo pode levar a vários problemas, incluindo redução da vida útil do rebolo, danos térmicos à peça de trabalho e redução geral da eficiência do desbaste. Aqui estão as possíveis causas e soluções para lidar com problemas de superaquecimento:
Parâmetros de moagem incorretos:
Causa:O uso de parâmetros de retificação inadequados, como velocidade, taxa de avanço ou profundidade de corte excessivas, pode gerar calor excessivo.
Solução:Ajuste os parâmetros de moagem dentro da faixa recomendada. Consulte as instruções do fabricante para obter as configurações ideais com base no material a ser moído.
Resfriamento ou lubrificação inadequados:
Causa:O uso insuficiente de refrigerante ou fluido de retificação pode resultar em aumento de atrito e calor.
Solução:Garanta um suprimento adequado de líquido de arrefecimento ou lubrificante durante o processo de retificação. O resfriamento adequado ajuda a dissipar o calor e previne danos térmicos.
Seleção incorreta de roda:
Causa:Escolher uma roda de desbaste com especificações inadequadas para o material a ser desbastado pode causar superaquecimento.
Solução:Selecione um rebolo com o tipo de abrasivo, tamanho de grão e liga corretos para a aplicação específica. A escolha adequada do rebolo ao material minimiza a geração de calor.
Problemas com o material da peça de trabalho:
Causa:Alguns materiais, especialmente aqueles com baixa condutividade térmica, são mais propensos a superaquecimento durante a retificação.
Solução:Ajuste os parâmetros de retificação para materiais com menor condutividade térmica. Considere usar um rebolo específico, projetado para materiais sensíveis ao calor.
Problemas de acabamento de rodas:
Causa:Irregularidades ou desgaste inadequado da roda de desbaste podem causar contato irregular e acúmulo de calor.
Solução:Rebolo regularmente para manter sua forma e remover qualquer brilho ou resíduos acumulados. Discos devidamente retificados garantem um desempenho de retificação consistente.
Manutenção inadequada da máquina:
Causa:Máquinas de moagem mal conservadas podem contribuir para problemas de superaquecimento.
Solução:Realize a manutenção regular da retificadora, incluindo a verificação dos sistemas de refrigeração, a inspeção do equipamento de retificação de rodas e o alinhamento adequado. Resolva quaisquer problemas mecânicos imediatamente.
Fluxo insuficiente de líquido de arrefecimento da roda:
Causa:O fluxo inadequado de refrigerante para a zona de retificação pode resultar em redução da dissipação de calor.
Solução:Verifique e otimize o sistema de fornecimento de refrigerante. Certifique-se de que o refrigerante chegue efetivamente à zona de retificação para manter a eficiência do resfriamento.
Tempo de moagem excessivo:
Causa:Sessões prolongadas de moagem sem pausas podem contribuir para o acúmulo de calor.
Solução:Implemente retificação intermitente e permita pausas para evitar o acúmulo excessivo de calor. Essa abordagem é particularmente importante para tarefas de retificação grandes ou desafiadoras.
Resolver problemas de superaquecimento na retificação requer uma abordagem abrangente, envolvendo a configuração adequada do equipamento, parâmetros de retificação adequados e práticas regulares de manutenção. Os operadores devem monitorar e controlar a geração de calor durante o processo de retificação para garantir desempenho ideal, vida útil prolongada da ferramenta e resultados de alta qualidade.
Preocupações com vibração
A vibração excessiva durante operações de retificação pode levar a diversos problemas, incluindo redução da qualidade da superfície, aumento do desgaste da ferramenta e possíveis danos à retificadora. Lidar com as preocupações com a vibração é crucial para alcançar processos de retificação precisos e eficientes. Aqui estão as possíveis causas e soluções para mitigar os problemas de vibração:
Desgaste irregular das rodas:
Causa:O desgaste irregular da roda de desbaste pode resultar em contato irregular com a peça de trabalho, causando vibrações.
Solução:Inspecione e limpe regularmente o rebolo para manter uma superfície consistente e plana. A manutenção adequada do rebolo ajuda a minimizar as vibrações.
Roda de desbaste desbalanceada:
Causa:Um desequilíbrio na roda de desbaste, seja por desgaste irregular ou defeitos de fabricação, pode causar vibração.
Solução:Balanceie o rebolo com uma balanceadora de rodas. O balanceamento garante uma distribuição uniforme do peso e reduz as vibrações durante a operação.
Calibração inadequada da máquina:
Causa:A calibração incorreta ou o desalinhamento dos componentes da máquina, como o eixo da roda ou a mesa de trabalho, podem contribuir para vibrações.
Solução:Calibre e alinhe regularmente os componentes da máquina para garantir o funcionamento adequado. Siga as instruções do fabricante para configuração e alinhamento da máquina.
Desequilíbrio da peça de trabalho:
Causa:Uma peça de trabalho irregular ou mal fixada pode criar desequilíbrio e induzir vibrações.
Solução:Fixe a peça de trabalho corretamente, garantindo que esteja posicionada e fixada uniformemente. Resolva quaisquer problemas de desequilíbrio antes de iniciar o processo de retificação.
Seleção incorreta de roda:
Causa:Usar uma roda de amolar com especificações inadequadas pode resultar em vibrações.
Solução:Selecione um rebolo com o tipo de abrasivo, tamanho de grão e liga adequados para o material a ser lixado. A escolha adequada do rebolo para a aplicação minimiza as vibrações.
Desgaste da máquina:
Causa:Componentes da máquina desgastados ou danificados, como rolamentos ou fusos, podem contribuir para vibrações.
Solução:Inspecione e substitua regularmente as peças desgastadas da máquina. A manutenção adequada ajuda a prevenir vibrações excessivas e prolonga a vida útil da retificadora.
Fluxo de refrigerante inadequado:
Causa:Fluxo insuficiente de refrigerante para a zona de retificação pode resultar em acúmulo de calor e vibrações.
Solução:Otimize o sistema de fornecimento de líquido de arrefecimento para garantir o resfriamento adequado. Um resfriamento eficaz reduz o risco de expansão e contração térmica, que podem levar a vibrações.
Problemas com o porta-ferramentas:
Causa:Problemas com o suporte da ferramenta ou com a interface do fuso podem causar vibrações.
Solução:Certifique-se de que o porta-ferramentas esteja firmemente montado e alinhado corretamente com o eixo. Utilize porta-ferramentas de alta qualidade e com manutenção adequada para minimizar as vibrações.
Fundação da Máquina:
Causa:Uma base de máquina precária ou suporte inadequado podem amplificar as vibrações.
Solução:Certifique-se de que a retificadora esteja instalada sobre uma base estável e adequadamente projetada. Resolva quaisquer problemas estruturais para minimizar as vibrações transmitidas à máquina.
Lidar eficazmente com problemas de vibração na retificação requer uma combinação de manutenção adequada da máquina, seleção de rebolos e manuseio das peças. Os operadores devem implementar práticas regulares de inspeção e manutenção para identificar e resolver problemas prontamente, resultando em melhor desempenho e qualidade da retificação.
Problemas de carregamento na moagem
A sobrecarga na retificação refere-se ao fenômeno em que os espaços entre os grãos abrasivos no rebolo são preenchidos com material sendo retificado, resultando em redução da ação de corte e aumento do atrito. A sobrecarga pode impactar negativamente a eficiência e a qualidade do processo de retificação. Aqui estão as possíveis causas e soluções para resolver problemas de sobrecarga:
Material da peça macia:
Causa:A trituração de materiais macios pode levar ao rápido entupimento dos grãos abrasivos.
Solução:Utilize um rebolo com granulação mais grossa e estrutura aberta ao trabalhar em materiais mais macios. Isso ajuda a evitar o acúmulo rápido de cavacos e permite a remoção eficiente de cavacos.
Contaminação do material:
Causa:Contaminantes presentes no material da peça de trabalho, como óleos, graxas ou resíduos de refrigerante, podem contribuir para o carregamento.
Solução:Garanta a limpeza adequada da peça de trabalho antes do desbaste para remover contaminantes. Use fluidos de corte ou refrigerantes adequados para minimizar a carga.
Aplicação incorreta do líquido de arrefecimento:
Causa:A aplicação inadequada ou imprópria do líquido de arrefecimento pode levar à lubrificação e ao resfriamento insuficientes, resultando em sobrecarga.
Solução:Otimize o fluxo e a concentração do líquido refrigerante. Garanta que o líquido refrigerante chegue efetivamente à zona de retificação para lubrificar e resfriar o processo, evitando sobrecarga.
Nitidez insuficiente da roda:
Causa:Discos de desbaste cegos ou desgastados são mais propensos a sofrer carga, pois perdem a eficiência de corte.
Solução:Afie e desbaste regularmente o rebolo para mantê-lo afiado. Use um afiador de rebolos para expor grãos abrasivos frescos e melhorar o corte.
Baixa velocidade da roda:
Causa:Operar a roda de moagem em baixa velocidade pode não fornecer força centrífuga suficiente para ejetar cavacos, causando carregamento.
Solução:Certifique-se de que a retificadora opere na velocidade recomendada para a combinação específica de disco e peça. Velocidades mais altas podem ajudar a remover melhor os cavacos.
Pressão excessiva:
Causa:Aplicar muita pressão durante a retificação pode forçar o material para dentro da roda, causando carga.
Solução:Use uma pressão de retificação moderada e consistente. Ajuste a taxa de avanço para permitir que o disco corte com eficiência, sem pressão excessiva que cause sobrecarga.
Especificações de roda erradas:
Causa:Usar uma roda de desbaste com especificações incorretas para o material a ser desbastado pode resultar em carga.
Solução:Selecione um rebolo com o tipo de abrasivo, tamanho de grão e liga adequados para a aplicação específica. A escolha adequada do rebolo ao material ajuda a evitar a formação de crostas.
Limpeza inadequada do líquido de arrefecimento:
Causa:Líquido de arrefecimento contaminado ou velho pode contribuir para problemas de carregamento.
Solução:Limpe e substitua o líquido de arrefecimento regularmente para evitar o acúmulo de contaminantes. Um líquido de arrefecimento novo e limpo melhora a lubrificação e o resfriamento, reduzindo a probabilidade de sobrecarga.
Técnica de curativo inadequada:
Causa:O desgaste incorreto da roda de desbaste pode causar irregularidades e carga.
Solução:Ajuste a roda corretamente usando a ferramenta de ajuste apropriada. Certifique-se de que o perfil da roda seja consistente e livre de irregularidades para evitar sobrecarga.
Abordar eficazmente os problemas de carga envolve uma combinação de seleção adequada de rodas, configuração da máquina e práticas de manutenção. Os operadores devem seguir os procedimentos recomendados, utilizar parâmetros de retificação adequados e implementar a retificação regular das rodas para minimizar a carga e otimizar o desempenho da retificação.
Escolher o disco de desbaste certo é crucial para obter resultados ideais em diversas aplicações de metalurgia e fabricação. A escolha depende de fatores como o material a ser trabalhado, o acabamento desejado e o tipo de desbaste utilizado.
Escolhendo o disco de moagem certo
Compatibilidade de materiais:
Metais ferrosos (aço, ferro):Utilize discos de desbaste projetados especificamente para metais ferrosos. Esses discos geralmente contêm abrasivos adequados à dureza do aço e são menos propensos a desgaste.
Metais não ferrosos (alumínio, latão):Escolha discos com abrasivos adequados para metais mais macios para evitar entupimentos. Discos de óxido de alumínio ou carboneto de silício são escolhas comuns.
Material abrasivo:
Óxido de alumínio:Adequado para retificação geral de metais ferrosos. É durável e versátil.
Alumina de zircônia:Oferece maior eficiência de corte e longevidade, tornando-o adequado para desbaste agressivo em metais ferrosos e não ferrosos.
Carboneto de silício:Ideal para lixar metais não ferrosos e pedras. É mais afiado, mas menos durável que o óxido de alumínio.
Tamanho do grão:
Grão grosso (24-36):Remoção rápida de material e retificação pesada.
Grão médio (40-60):Equilibra a remoção de material e o acabamento da superfície.
Grão fino (80-120):Proporciona um acabamento suave, adequado para preparação de superfícies e lixamento leve.
Tipo de roda:
Tipo 27 (Centro Deprimido):Disco de desbaste padrão com superfície plana, ideal para desbaste de superfícies e trabalhos de bordas.
Tipo 29 (Cônico):Design angulado para remoção agressiva de material e melhor mistura de superfície.
Tipo 1 (Reto):Utilizado para aplicações de corte. Oferece um perfil fino para cortes precisos.
Aplicativo:
Moagem:Discos de desbaste padrão para remoção e modelagem de material.
Corte:Use discos de corte para cortar metal, proporcionando um fio reto e limpo.
Discos de aba:Combine lixamento e acabamento em um só produto. Adequado para misturar e alisar superfícies.
Compatibilidade com Grinder:
Certifique-se de que o disco de moagem seja compatível com o tipo e a velocidade da lixadeira utilizada. Verifique as recomendações do fabricante para a rotação máxima do disco (RPM).
Especificidade da tarefa:
Remoção de estoque pesado:Escolha uma lixa de granulação grossa e um disco tipo 27 ou tipo 29 para uma remoção eficiente do material.
Acabamento de superfície:Opte por lixas de granulação média a fina com discos de aba para acabamentos mais suaves.
Considerações de segurança:
Siga as orientações de segurança, incluindo o uso de equipamentos de proteção individual (EPI) adequados, como óculos de segurança e luvas.
Escolha discos reforçados para maior durabilidade e segurança.
Marca e Qualidade:
Selecione discos de marcas renomadas, conhecidas pela qualidade e consistência. Discos de alta qualidade oferecem melhor desempenho e durabilidade.
Consideração de custos:
Equilibre o custo inicial com a vida útil e o desempenho esperados do disco de desbaste. Discos de alta qualidade podem ter um custo inicial mais alto, mas podem oferecer melhor custo-benefício ao longo do tempo.
Ao considerar esses fatores, os operadores podem escolher o disco de desbaste certo para suas aplicações específicas, garantindo eficiência, segurança e resultados ideais.
Conclusão
Concluindo, a seleção do disco de desbaste adequado é um aspecto crucial para alcançar resultados bem-sucedidos em usinagem e fabricação de metais. A escolha depende de vários fatores, como o material a ser trabalhado, o acabamento desejado e o tipo de retificadora utilizada. Ao considerar a compatibilidade do material, o tipo de abrasivo, o tamanho do grão, o tipo de rebolo, a aplicação, a compatibilidade da retificadora, a especificidade da tarefa, a segurança, a qualidade da marca e o custo, os operadores podem tomar decisões informadas para aumentar a eficiência e a segurança em seus processos de retificação.
É essencial seguir as diretrizes de segurança, usar equipamentos de proteção individual adequados e seguir as recomendações do fabricante quanto à compatibilidade entre a retificadora e o disco. Seja para remoção de material pesado, acabamento de superfícies ou aplicações de corte, o disco de retificação certo pode impactar significativamente a qualidade e a eficiência do trabalho.
Além disso, verificações periódicas de desgaste, resolução de problemas como superaquecimento e vibração e compreensão de problemas de carga contribuem para prolongar a vida útil do disco de moagem e garantir um desempenho consistente.
Em resumo, uma abordagem bem informada e sistemática para selecionar, usar e manter discos de desbaste é essencial para alcançar resultados ideais, aumentar a produtividade e garantir um ambiente de trabalho seguro.
Horário da postagem: 12/01/2024